How Manufacturing Execution Systems Are Transforming the Sector

The fast-paced industrial scene of today calls for efficiency, openness, and real-time decision-making more than it does ever have. Manufacturers are always looking for strategies to maximize their operations, lower expenses, and raise the caliber of their products. Now enter Manufacturing Execution Systems (MES), a revolutionary technology altering manufacturing operations. From big-scale industrial plants to small-scale workshops, MES is becoming a vital instrument for contemporary production. But precisely what is a Manufacturing Execution System, and why is it so important for manufacturing going forward? Let us now delve in.
MES, or manufacturing execution systems, are what?
A Manufacturing Execution System (MES) is a digital solution meant to close the gap between the shop floor and systems of enterprise-level planning such as ERP. It gives manufacturers real-time view of manufacturing processes so they may monitor, manage, and maximize their operations. Consider it as the core nervous system of a manufacturing plant—it gathers information from workers, machines, and processes and converts it into practical insights.
MES transcends just gathering facts. To offer a whole picture of the whole production lifetime, it connects with other systems such Manufacturing Information Systems (MIS). From acquisition of raw materials to last product delivery, MES guarantees that every stage is tracked, examined, and improved.
The Why of Manufacturing Execution Systems’ Trend
Driven by Industry 4.0 and the Internet of Things (IoT), the industrial sector is having a digital revolution. Demand for sophisticated solutions like MES is rising as factories grow smarter and more linked. Here is the rationale:
Real-time data for decisions made right now
Manufacturers used periodic reports and hand data entry in the past to track output. Delays, mistakes, and lost possibilities followed from this often. Real-time data collecting made possible by MES lets management make quick decisions based on need. Whether it’s reallocating resources, changing machine settings, or clearing obstacles, MES helps manufacturers to act fast and forcefully.
Enhanced Quality Management
For every manufacturer, quality ranks highest. MES monitors every phase of the manufacturing process to help to preserve constant quality. Should a flaw be found, the system can set off alarms and possibly stop output until the problem is fixed. By means of this proactive strategy, rework is minimized, waste is minimized, and only premium items guarantee reach to consumers.
Improved Followability
Traceability is absolutely essential in sectors such food manufacture, autos, and medicines. MES offers end-to- end visibility, enabling producers to follow every item from beginning to completion. For handling recalls or quality problems as well as for regulatory standard compliance, this is extremely crucial.
Better Productivity and Efficiency
MES reduces inefficiencies and increases output by automating regular chores and streamlining processes. The system manages data collecting, reporting, and analysis; workers may concentrate on value-added operations. Along with accelerating output, this lowers labor costs.
Complementing Manufacturing Information Systems
MES doesn’t function alone. It offers a whole picture of operations working hand-in-hand with Manufacturing Information Systems (MIS). MES handles execution and monitoring; MIS concentrates on higher-level planning and resource management. All taken together, they produce a flawless information flow across the company.
The User View: How MES Helps Manufacturers
From the standpoint of a manufacturer, putting a Manufacturing Execution System into use is a calculated investment. The following shows how it affects several stakeholders:
Plant managers sometimes have several duties, from guaranteeing worker safety to fulfilling production goals. MES streamlines their work by giving a consolidated platform to track every facet of the manufacturing process. Real-time dashboards and alarms help them to see problems before they become more serious and enable data-driven decisions to maintain seamless operations.
MES is a great technology that improves daily duties for employees on the manufacturing floor. By use of the system, they can obtain digital work orders, machine settings, and quality checklists rather of depending on paper-based instructions or human data entry. This lessens mistakes, enhances communication, and simplifies and speeds their employment.
Accurate data is what Quality Assurance Teams depend on to make sure items satisfy criteria. MES gives them comprehensive records of every manufacturing run including machine data, material use, and inspection findings including machine settings. This not only makes audits easier but also points up areas needing work and trends.
For executives:
MES offers an executive level bird’s-eye perspective on activities. Integrating with Manufacturing Information Systems provides insights into key performance indicators (KPIs) including production efficiency, downtime, and general equipment effectiveness (OEE). This helps leaders to make strategic choices promoting profitability and expansion.
Difficulties and Thinkthroughs
MES has clearly benefits, but putting the system into use is not without difficulties. These factors should help manufacturers:
Beginning Investment
Using a MES calls for a large upfront outlay in hardware, software, and training. Still, the long-term return on investment—in terms of more efficiency, lower waste, and better quality—often exceeds the starting expenses.
Integration with Outstanding Systems
Many manufacturers still depend on outdated systems that might not be fit for contemporary MES solutions. Although combining these systems can be difficult and time-consuming, flawless operations depend on it.
Managing Change
Using MES usually calls for a cultural change inside the company. Managers and employees must be taught how to properly operate the system; change could run against opposition. Overcoming these difficulties mostly depends on constant support and open communication.
Manufacturing Execution Systems: Looking Forward
Manufacturing execution systems will change along with technology. These developments are worth observing:
Machine learning and artificial intelligence
MES solutions driven by artificial intelligence will support sophisticated analytics, anomaly detection, and predictive maintenance. Learning from past data helps these systems predict problems and suggest best responses.
MES from the Cloud
Because of their scalability, adaptability, and economy, cloud-based MES systems are becoming more and more appealing. They enable manufacturers to access real-time data from anywhere, therefore transforming remote monitoring and management into reality.
Improved Cyberspace
Cybersecurity will take front stage as MES is increasingly linked. Strong security measures will be required of manufacturers to guard private information and guarantee system integrity.
Sustainability and Green Manufacturing
MES will be very important for manufacturers to reach their environmental targets. It promotes green production techniques by best using resources and cutting waste.
Conclusion
For manufacturers who wish to remain competitive in the digital era of today, Manufacturing Execution Systems are no more a luxury; they are rather a need. MES is transforming manufacturing by giving real-time visibility, bettering quality control, and increasing efficiency. Integrated with Manufacturing Information Systems, it generates a strong ecosystem promoting innovation and expansion.
What's Your Reaction?
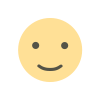

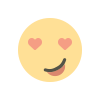
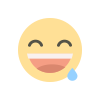
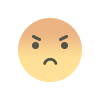
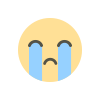
