The Technology Behind Cup Sealing Machines
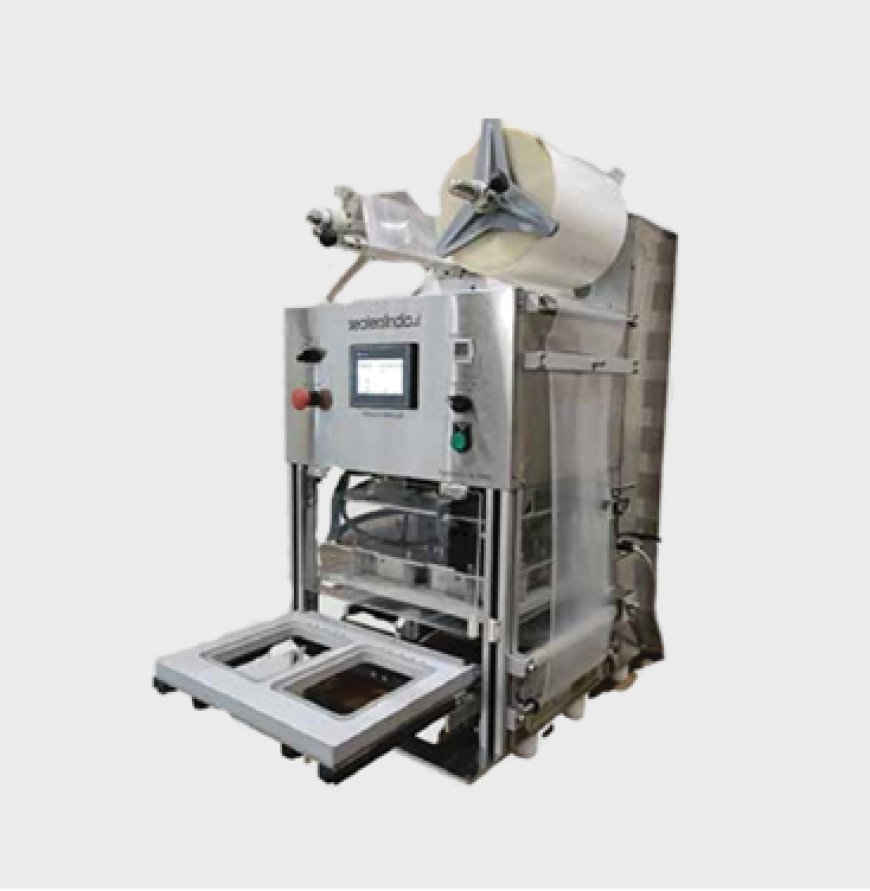
In today’s fast-paced world, the food and beverage industry relies heavily on automation to streamline processes, increase efficiency, and maintain high standards of hygiene. One of the key technologies that plays a crucial role in achieving this is the Cup Sealing Machine. Whether it's a juice box, milk tea, or a to-go cup of coffee, the need for a secure, leak-proof seal has never been more vital. Cup sealing machines provide the solution to this problem by ensuring that the contents of the cup remain fresh, uncontaminated, and spill-proof, which is essential for both consumer convenience and product safety.
While a Tray Sealing Machine is often used for sealing pre-formed trays containing various food products, cup sealing machines focus on individual cups or containers. This blog explores the technology behind cup sealing machines and how they ensure that your beverages are leak-proof and safe for transport, offering an in-depth look into their functionality, components, and the role they play in the food and beverage industry.
Understanding the Importance of a Leak-Proof Seal
Before diving into the technology, it’s important to understand why a leak-proof seal is so crucial, especially in the food and beverage industry. A Cup Sealing Machine ensures that the liquid or product inside the cup stays contained, preventing spillage, contamination, and spoilage. This is particularly important in an environment where beverages are being transported, whether it's for delivery, take-out, or even just to ensure the integrity of the product during the point of sale.
A faulty seal can lead to several issues:
Spillage: Inadequate seals allow liquids to escape, leading to messes, loss of product, and customer dissatisfaction.
Contamination: Without a proper seal, external factors like dust, dirt, and bacteria could contaminate the contents.
Loss of Freshness: For products like smoothies, milk tea, or juices, a good seal helps retain the freshness and prevents oxidation or contamination from the air.
Brand Reputation: In the highly competitive food and beverage market, a damaged seal can have serious consequences, including harm to a company’s reputation and customer trust.
Thus, ensuring that a cup is properly sealed is not just a matter of convenience; it's also a matter of product integrity and safety.
How Cup Sealing Machines Work
A Cup Sealing Machine is designed to automatically seal the top of a cup or container, typically made of plastic or paper, with a film or lid. The primary purpose of this machine is to ensure that the seal is airtight, leak-proof, and tamper-evident. The technology behind these machines involves a series of steps and components that come together to perform the sealing process efficiently.
1. Cup Placement and Alignment
The first step in the sealing process is the precise placement of the cup onto the machine. The cups are generally placed on a conveyor system that automatically aligns them for the sealing process. This ensures that the cups are in the correct position before the sealing film is applied. Accurate alignment is crucial to avoid mis-sealing, which could lead to leakage.
2. Film or Lid Application
Once the cups are aligned, the next step is the application of the sealing film or lid. The film, typically made of food-grade plastic or aluminium, is pulled over the top of the cup. This film is specifically chosen based on the type of beverage or product that the cup is holding. For example, drinks like smoothies or milk tea may require a thicker, more robust film to prevent leaks, while other products may use a thinner film.
In some cases, a Tray Sealing Machine is used, which functions similarly to a cup sealer but is designed to seal larger trays or containers. These machines often use a combination of heat and pressure to create an airtight seal.
3. Sealing Mechanism
Once the film is in place, the machine uses a combination of heat and pressure to bond the film to the edge of the cup, creating a hermetic seal. The sealing head of the Cup Sealing Machine typically includes a heating element and a sealing die, which works together to create the bond.
The heating element heats the film to the correct temperature, softening it and allowing it to adhere to the cup. At the same time, the sealing die applies pressure to ensure that the film bonds securely with the cup. This process ensures that the seal is not only leak-proof but also tamper-evident, meaning that if someone tries to open the cup, it will be visibly damaged.
4. Cooling and Ejection
After the seal is created, the cup moves through a cooling section where the bond is allowed to solidify. Cooling is important to ensure that the seal is strong and long-lasting. Once the seal is sufficiently cooled, the sealed cups are automatically ejected from the machine, ready for packaging, storage, or sale.
In some cases, additional features such as perforation or punching are applied to the film, allowing customers to easily peel off the top layer when consuming the beverage.
Key Components of a Cup Sealing Machine
A Cup Sealing Machine is made up of several critical components that work together to ensure a high-quality, leak-proof seal. These components include:
1. Heating Element
The heating element is responsible for generating the heat required to soften the sealing film. It must be carefully calibrated to reach the ideal temperature for the film material being used. Too much heat can damage the film, while too little can result in weak seals.
2. Sealing Die
The sealing die is the part of the machine that applies pressure to the film once it is heated. The die is typically made of metal and is custom-designed to fit the specific cup size and shape being used. It ensures that the film is pressed tightly against the cup, creating an airtight seal.
3. Film Roll
The film roll is the material used to create the seal. This film is typically made of food-safe plastics or laminates that provide durability and leak-proof properties. The film can be customized with branding, barcodes, or nutritional information to enhance the product's appeal.
4. Conveyor System
The conveyor system is responsible for moving the cups through each stage of the sealing process. It ensures that each cup is aligned properly and transferred smoothly from one step to the next, increasing the machine's efficiency.
5. Control Panel
Modern Cup Sealing Machines are equipped with digital control panels that allow operators to adjust settings like temperature, pressure, and speed. This flexibility ensures that the machine can be used with different cup sizes and film materials, optimizing performance.
Technologies Used in Tray Sealing Machines
While Tray Sealing Machines are similar in function to cup-sealing machines, they are designed to seal larger containers. Tray-sealing machines are commonly used in the packaging of meals, snacks, and other ready-to-eat foods. These machines use a similar sealing process but are capable of sealing multiple trays simultaneously or large trays, often incorporating vacuum sealing or modified atmosphere packaging (MAP) to extend shelf life and preserve the quality of the food.
Tray sealing machines work in the same way as cup sealing machines, utilizing heat and pressure to form a tight, leak-proof seal. However, tray sealing machines also include the additional capability to remove air from the tray before sealing (in vacuum packaging), which helps to preserve the freshness of food for longer periods.
The Role of Innovation in Cup Sealing Machines
As the demand for faster, more efficient packaging solutions grows, cup-sealing machine manufacturers are constantly innovating. These innovations not only focus on increasing speed and efficiency but also on improving the overall quality and functionality of the seal. Some of the latest advancements in cup sealing technology include:
Smart Technology: Newer cup sealing machines incorporate advanced sensors and artificial intelligence (AI) to monitor the sealing process in real time, ensuring that every seal is perfect and within the required specifications.
Eco-friendly Materials: Many manufacturers are exploring more sustainable materials for sealing films, including biodegradable and recyclable plastics.
Increased Automation: Automation is being integrated into cup sealing machines, allowing for faster processing times, less human error, and greater consistency.
Multiple Seal Options: Modern machines can offer different types of seals, including peelable seals and tamper-evident seals, catering to a broader range of packaging requirements.
Conclusion
The Cup Sealing Machine is an essential piece of equipment for the food and beverage industry, ensuring that products are securely sealed, leak-proof, and safe for transport. Through its precise combination of heat, pressure, and careful control, a cup sealing machine creates an airtight seal that guarantees freshness, prevents spillage, and ensures product integrity. When coupled with innovations like smart sensors and eco-friendly materials, the technology behind cup-sealing machines continues to evolve, offering even greater efficiency and sustainability.
In contrast, Tray Sealing Machines also play a significant role in the packaging industry, particularly for ready-to-eat meals, by applying similar sealing techniques to larger containers. Both machines contribute to the broader goal of improving the food packaging process and making sure that products are delivered in the best possible condition.
For anyone working in food packaging, beverage production, or any industry that requires secure, leak-proof seals, understanding the technology behind Cup Sealing Machines and Tray Sealing Machines is essential to maintaining high standards of quality and safety.
What's Your Reaction?
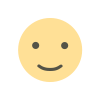

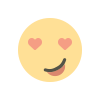
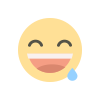
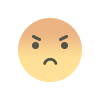
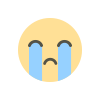
